At Align Aerospace, our policy is to provide customers on-time delivery of defect-free products and services. We are committed to the continuous improvement of our quality systems and processes.
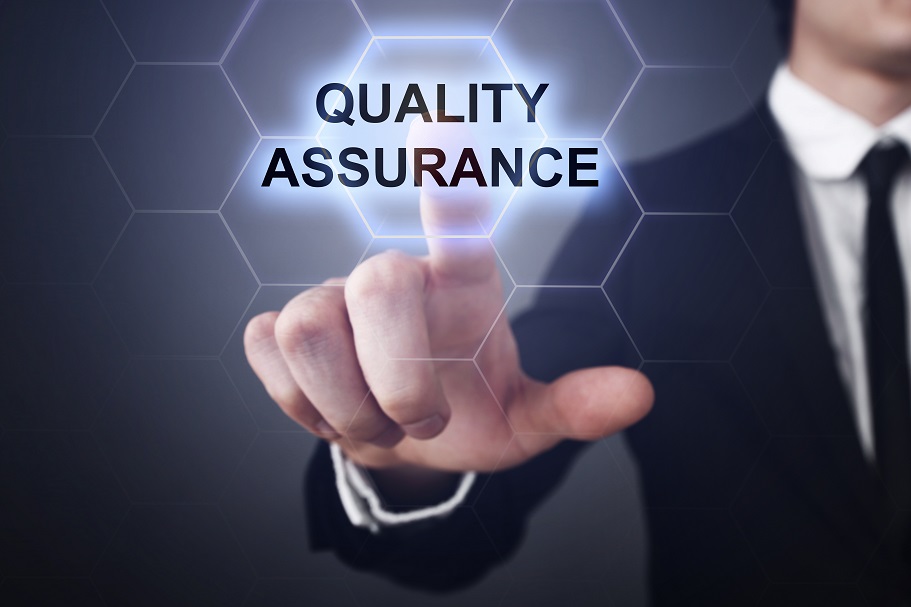
We work closely with suppliers to improve process controls to reduce non-conformance. Key criteria are monitored during manufacturing to immediately correct any anomalies and delegated inspection is a necessary component of of an overall cost reduction strategy as it eliminates the cost of redundant receiving inspections.
Some examples of our value-added quality services include:
- – Incoming inspection of every shipment
- – AS13001 certified inspectors for delegated inspection
- – Dock-to-stock delivery
- – Dedicated customer quality representatives who are process and product experts
- – Process certification ensures predictable output
- – Continuous training and state of the art equipment to meet customer quality requirements.
- – Digital storage of product certifications, inspection, and test reports
- – Chemical and physical properties testing to ensure compliance to customer specifications
- – Use of approved independent test labs for customer specs conformance validation